The MSG TURBO-AIR COOLED 2000 is a great match for almost any location and conditions. The air-cooled design eliminates the installation restrictions and the utility costs associated with water-cooled units by removing the cost of pumping and treating water, and maintaining the water system.
RELIABLE CENTRIFUGAL COMPRESSOR – NOW AVAILABLE AIR COOLED
The MSG TURBO-AIR COOLED 2000 centrifugal compressor is designed for applications where there is a limited supply or no water available for cooling.
The MSG TURBO-AIR COOLED compressor makes it possible for more industries around the world to enjoy all the advantages of our state-of-the-art centrifugal compressor design.
Ytterligare resurser
Operating Comparison: Air vs. Water Cooled
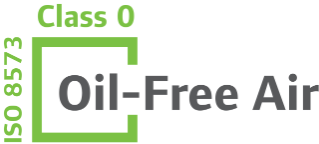
ISO CERTIFIED CLASS 0
The MSG TURBO-AIR centrifugal compressor product line has been engineered to produce oil-free air for more than 60 years. This certification officially acknowledges the ability of our compressors to produce 100% oil-free air, providing our customers with enhanced quality assurance.
BENEFITS OF MSG TURBO-AIR COMPRESSORS:
ISO 8573-1 Certified Oil-Free Air
- Prevents oil contamination of your system
- Limits the potential for compressed air pipeline fires caused by oil carryover
- Eliminates costly waste disposal problems associated with oil-laden condensate
- Eliminates the expense and associated maintenance requirements of oil-removal filters, since no oil enters the compressed air stream in the compressor
Simple Installation
- True unloading capability helps to take advantage of opportunities for energy savings
- Increased uptime compared to alternative technologies translates into reduced operating life-cycle costs
- Reduced number of external connections
- Compact design reduces required floor space
- Meets OSHA's sound level requirements without sound enclosure
Low-Cost Operation
- True unloading capability helps to take advantage of opportunities for energy savings
- Increased uptime compared to alternative technologies translates into reduced operating life-cycle costs
- Excellent part-load efficiencies for any operating load
- No sliding or rubbing parts in the compression process causing wear or efficiency loss
Easy Operation
- The MAESTRO™ Universal control panel provides a built-in web server, allowing compressor monitoring using your local intranet/span>
- Significant annual savings in operating cost by providing more precise control
- Easy-to-use, automatic operation
Easy Maintenance
- Compression elements do not wear or require periodic replacement
- No oil-removal filters to clean or replace
- Accessible, horizontally split gearbox for quick inspection
- Intercooler and aftercooler bundles are easy to remove for inspection and cleaning
- Water-in-tube design intercooler and aftercooler allow for simple mechanical cleaning
- Maintenance-free dry coupling
High Reliablity
- Thrust loads absorbed at low speed
- Non-contacting air and oil seals
- Stainless steel compression elements
- Conservative, high-quality gear design
- Extended life pinion bearing design
- Centrifugal compressors are proven to have a long mean time between failures (MTBF), and independent research has shown an industry-leading availability of 99.7%
MSG TURBO-AIR COOLED 2000 Centrifugal Compressors 3-stage Compressor Layout
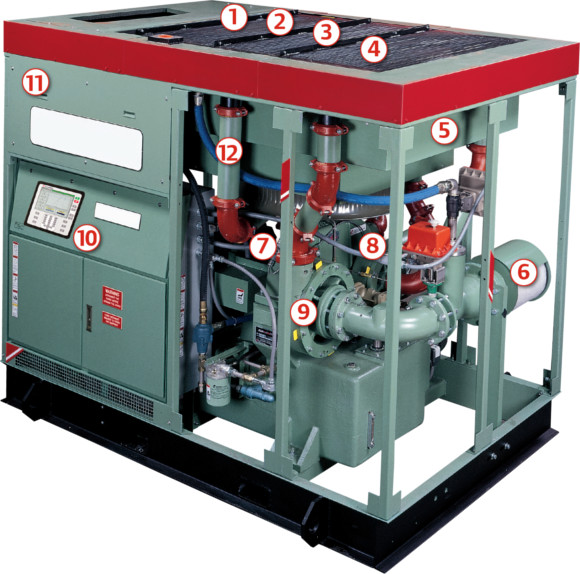
- Oil Cooler: Air-cooled heat exchanger for lubrication system
- Aftercooler: Air-cooled heat exchanger for 3 rd stage discharge air
- 2 nd Stage Intercooler: Air-cooled heat exchanger for 2 nd stage discharge air
- 1st Stage Intercooler: Air-cooled heat exchanger for 1st stage discharge air
- Fan Plenum & Cooler Fan: Fan and plenum to facilitate air-cooled heat transfer
- Inlet Filter: Removes airborne particulate prior to 1st compression stage
- 3rd Stage of Compression: Final compression stage to reach pressure set point
- 2nd Stage of Compression: Intermediary compression stage before final compression stage
- 1st Stage of Compression: Initial compression stage of atmospheric air
- Control Center: Single-point electrical connection for MAESTRO Universal control panel, drive motor starter, and auxiliaries
- Sound Enclosure: Enclosure provides quiet operation at 85 dBA
- Compressor Discharge: Discharge from final compression stage to aftercooler and subsequent downstream equipment